Data analysis Production Monitoring for the Food and Beverage Industry: A Complete Guide
Production monitoring in the food and beverage industry plays a crucial role in ensuring quality, safety, and efficiency. With growing regulatory requirements and consumer expectations for transparency, data analysis has become indispensable for optimizing production processes. This guide explores real-time data monitoring, compliance challenges, and technological advancements that are shaping the industry.
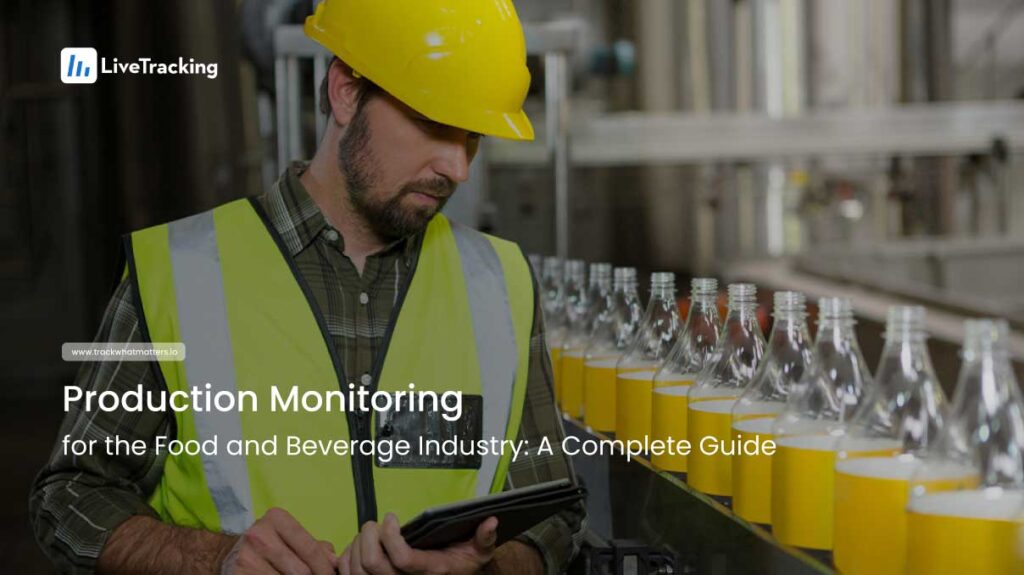
Production monitoring in the food and beverage industry has become an essential component of ensuring quality, safety, and efficiency. As the industry faces increasing regulatory scrutiny and consumer demand for transparency, effective monitoring systems are more critical than ever. This guide delves into the intricacies of production monitoring, exploring its significance, challenges, technological solutions, and real-world applications.
What Is Production Monitoring and Why Does It Matter?
Production monitoring refers to the systematic observation and evaluation of manufacturing processes within the food and beverage sector. This practice encompasses a range of activities, from tracking raw material inputs to assessing final product quality. The primary goal is to ensure that production meets established standards for safety, quality, and efficiency.
In an industry where safety is paramount, production monitoring serves as a safeguard against potential hazards. It enables manufacturers to identify deviations from standard operating procedures (SOPs) and rectify them before they lead to significant issues. Moreover, effective monitoring can enhance operational efficiency, reduce waste, and improve overall product quality, ultimately leading to increased customer satisfaction.
As consumers become more health-conscious and demand transparency regarding food sources and production methods, production monitoring plays a vital role in building trust. Companies that prioritize monitoring can provide verifiable evidence of their commitment to quality and safety, thereby enhancing their brand reputation.
Additionally, the integration of technology into production monitoring has revolutionized how manufacturers operate. Advanced systems, such as real-time data analytics and IoT (Internet of Things) devices, allow for continuous tracking of production metrics. This technological advancement not only streamlines the monitoring process but also enables predictive maintenance, where potential equipment failures can be anticipated and addressed before they disrupt production. Such proactive measures can lead to significant cost savings and minimize downtime, ensuring that production schedules remain on track.
Furthermore, regulatory compliance is another critical aspect of production monitoring. The food and beverage industry is subject to stringent regulations that vary by region and product type. By implementing robust monitoring systems, companies can ensure adherence to these regulations, thereby avoiding costly fines and potential legal issues. Regular audits and assessments, facilitated by effective monitoring, help maintain compliance while fostering a culture of accountability and continuous improvement within the organization.
Key Challenges in Food and Beverage Production Monitoring
While the benefits of production monitoring are clear, several challenges can impede its effective implementation. One of the most significant hurdles is the complexity of food production processes. With multiple stages involved—from sourcing raw materials to processing and packaging—monitoring each step requires a comprehensive understanding of the entire production cycle. Each phase has its own set of variables that can affect quality and efficiency, such as temperature control during storage, contamination risks during processing, and even the timing of packaging. This intricate web of operations necessitates a robust monitoring system that can adapt to the unique requirements of each stage, which can be a daunting task for many manufacturers.
Another challenge is the integration of monitoring systems with existing technologies. Many food and beverage manufacturers rely on legacy systems that may not be compatible with modern monitoring solutions. This lack of integration can lead to data silos, making it difficult to obtain a holistic view of production performance. Furthermore, the transition to new technologies often involves significant financial investment and employee training, which can disrupt ongoing operations. Manufacturers must weigh the costs and benefits of upgrading their systems against the potential for improved efficiency and compliance, creating a complex decision-making landscape.
Additionally, regulatory compliance poses a constant challenge. The food and beverage industry is heavily regulated, with strict guidelines governing everything from ingredient sourcing to labeling. Keeping up with these regulations requires continuous monitoring and documentation, which can be resource-intensive and time-consuming. Companies must not only ensure compliance with local laws but also navigate international regulations if they export their products. This adds another layer of complexity, as different countries may have varying standards and requirements. Moreover, the consequences of non-compliance can be severe, including hefty fines and damage to a brand’s reputation, making it imperative for manufacturers to stay vigilant and proactive in their monitoring efforts.
Moreover, the rapid pace of technological advancement presents both an opportunity and a challenge. While innovations such as IoT devices and AI-driven analytics can enhance monitoring capabilities, they also require a skilled workforce adept at utilizing these technologies effectively. The shortage of qualified personnel in the food and beverage sector can hinder the adoption of advanced monitoring solutions. Companies may find themselves in a race against time to upskill their workforce or risk falling behind competitors who are more agile in embracing new technologies. This talent gap can further complicate the implementation of comprehensive monitoring systems, as employees may struggle to interpret and act on the data generated by these advanced tools.
How Real-Time Data Improves Food Safety and Compliance
Real-time data collection and analysis have revolutionized production monitoring in the food and beverage industry. By leveraging IoT (Internet of Things) devices and sensors, manufacturers can gather data at every stage of production, allowing for immediate insights into operational performance.
This immediacy is crucial for food safety. For instance, temperature-sensitive products, such as dairy and meat, require constant monitoring to prevent spoilage. Real-time data enables manufacturers to respond quickly to any deviations, ensuring that products remain within safe temperature ranges throughout the supply chain. In addition to temperature, other critical factors such as humidity, pH levels, and contamination risks can also be monitored in real time. This comprehensive oversight not only helps in maintaining product integrity but also builds consumer trust, as they are increasingly aware of and concerned about food safety standards.
Moreover, real-time monitoring enhances compliance with regulatory standards. Automated systems can generate reports and documentation in real time, simplifying the compliance process. This not only reduces the risk of human error but also ensures that companies can provide accurate records during audits, thereby fostering a culture of accountability and transparency. Furthermore, the integration of advanced analytics allows businesses to predict potential compliance issues before they arise, enabling proactive measures to be taken. This predictive capability can significantly reduce the likelihood of costly recalls and legal repercussions, ultimately safeguarding both the brand’s reputation and consumer health.
In addition to these benefits, real-time data also facilitates better decision-making across the supply chain. By analyzing trends and patterns in the data collected, manufacturers can optimize production schedules, reduce waste, and improve resource allocation. For example, if a particular ingredient is consistently found to be out of specification, manufacturers can quickly adjust sourcing or processing methods to rectify the issue. This agility not only enhances operational efficiency but also contributes to sustainability efforts by minimizing waste and ensuring that only high-quality products reach consumers.
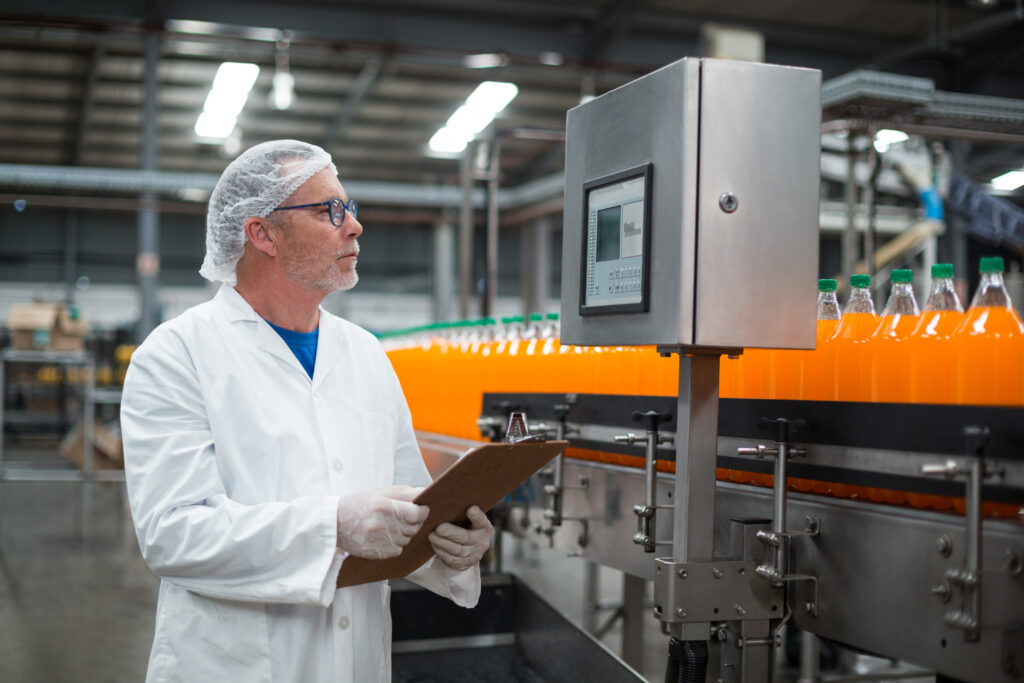
FAQ
1. How does data analysis improve food production monitoring?
Data analysis enables real-time tracking, enhances food safety, ensures regulatory compliance, and optimizes production efficiency.
2. What are the key challenges of implementing real-time monitoring?
Challenges include integration with legacy systems, regulatory complexity, and the need for a skilled workforce.
3. How can IoT improve food safety?
IoT sensors monitor temperature, humidity, and contamination risks, allowing manufacturers to respond immediately to potential issues.
4. What role does predictive maintenance play in food production?
Predictive maintenance prevents equipment failures, reducing downtime and costs through proactive monitoring.
5. How can companies ensure compliance with food safety regulations?
By using automated data analysis tools, businesses can track, document, and report compliance measures accurately.
Glossary
- IoT (Internet of Things): Smart devices that collect and share data.
- Predictive Maintenance: Preventing equipment failure through data analysis.
- Compliance: Adherence to food safety regulations.
- Data Silos: Isolated data that is difficult to integrate.
- Traceability: Tracking a product’s journey from production to consumer.
Share
Table of Content
Stay Up-to-Date
Get LiveTracking news in your inbox.
Error: Contact form not found.
By submitting this form I have read and acknowledged the Privacy Policy.
From the blog
The latest industry news, interviews, technologies, and resources.